不掌握这些知识,千万别说自己是机械可靠性工程师!
推广:由91质量网独家开发的,国内第一款具有完全自主知识产权的机械可靠性软件PROMREL 介绍:
Promrel(Professional Mechanical Reliability Analysis System ) 是一个与数字化环境集成的、支持开展可靠性与性能一体化设计的专业机械可靠性设计分析与优化软件。可针对机械、机电等复杂产品,进行结构、机构、设备、系统级产品概率设计、复杂环境下多场耦合、多机理相关的可靠性量化分析、多学科优化、寿命预测、可靠性设计方案优化等。了解更多内容请QQ:1401937020 咨询。
以下正文:
机械可靠性设计分析离不开疲劳强度设计相关知识,作为机械可靠性工程师,这些知识应该掌握。
疲劳强度设计
对承受循环应力的零件和构件,根据疲劳强度理论和疲劳试验数据,决定其合理的结构和尺寸的机械设计方法。机械零件和构件对疲劳破坏的抗力,称为零件和构件的疲劳强度。疲劳强度由零件的局部应力状态和该处的材料性能确定,所以疲劳强度设计是以零件最弱区为依据的。通过改进零件的形状以降低峰值应力,或在最弱区的表面层采用强化工艺,就能显著地提高其疲劳强度。
在材料的疲劳现象未被认识之前,机械设计只考虑静强度,而不考虑应力变化对零件寿命的影响。这样设计出来的机械产品经常在运行一段时期后,经过一定次数的应力变化循环而产生疲劳,致使突然发生脆性断裂,造成灾难性事故。应用疲劳强度设计能保证机械在给定的寿命内安全运行。疲劳强度设计方法有常规疲劳强度设计、损伤容限设计和疲劳强度可靠性设计。
简史 19世纪40年代,随着铁路的发展,机车车轴的疲劳破坏成为非常严重的问题。1867年,德国A.沃勒在巴黎博览会上展出了他用旋转弯曲试验获得车轴疲劳试验结果,把疲劳与应力联系起来,提出了疲劳极限的概念,为常规疲劳设计奠定了基础。
20世纪40年代以前的常规疲劳强度设计只考虑无限寿命设计。第二次世界大战中及战后,通过对当时发生的许多疲劳破坏事故的调查分析,逐渐形成了现代的常规疲劳强度设计,它非但提高了无限寿命设计的计算精确度,而且可以按给定的有限寿命来设计零件,有限寿命设计的理论基础是线性损伤积累理论。早在1924年,德国A.帕姆格伦在估算滚动轴承寿命时,曾假定轴承材料受到的疲劳损伤的积累与轴承转动次数(等于载荷的循环次数)成线性关系,即两者之间的关系可以用一次方程式来表示。1945年,美国M.A.迈因纳根据更多的资料和数据,明确提出了线性损伤积累理论,也称帕姆格伦-迈因纳定理。
随着断裂力学的发展,美国A.K.黑德于1953年提出了疲劳裂纹扩展的理论。1957年,美国P.C.帕里斯提出了疲劳裂纹扩展速率的半经验公式。1967年,美国R.G.福尔曼等又对此提出考虑平均应力影响的修正公式。这些工作使人们有可能计算带裂纹零件的剩余寿命,并加以具体应用,形成了损伤容限设计。
用概率统计方法处理疲劳试验数据,是20世纪20年代开始的。60年代后期,可靠性设计从电子产品发展到机械产品,于是在航天、航空工业的先导下,开始了可靠性理论在疲劳强度设计中的应用。
1961年联邦德国 H. 诺伊贝尔提出的关于缺口件中名义应力-应变与局部应力-应变之间的关系,称为诺伊贝尔公式。1968年加拿大 R.M. 韦策尔在诺伊贝尔公式的基础上,提出了估算零件裂纹形成寿命的方法,即局部应力-应变法,在疲劳强度设计中得到了应用和发展。
常规疲劳强度设计 假设材料没有初始裂纹,经过一定的应力循环后,由于疲劳损伤的积累,才形成裂纹,裂纹在应力循环下继续扩展,直至发生全截面脆性断裂。裂纹形成前的应力循环数,称为无裂纹寿命;裂纹形成后直到疲劳断裂的应力循环数,称为裂纹扩展寿命。零件总寿命为两者之和。
根据零件所用材料的试样的疲劳试验结果,以最大应力σ为纵坐标、以达到疲劳破坏的循环数 N为横坐标,画出一组试样在某一循环特征下的应力-寿命曲线(σ-N曲线)。应力-寿命曲线和应变-寿命曲线统称为S-N 曲线(图1)。曲线的斜线部分的一般表达式为:σmN=C,式中m和C为材料常数。在应力和循环数的双对数坐标中,该方程式的图形是一条直线。
大多数结构钢,当σ值降低到一定限度时,不再发生疲劳破坏,即疲劳寿命是无限的,这时在图中出现了水平线段。这个σ值,即转折点Μ的应力值,称为材料的疲劳极限,它比静强度低很多。Μ点的循环数,称为循环基数,用符号N 0表示。N 0将S-N 曲线分成两部分。其右边的区域,N≥N 0为无限寿命区;左边的区域,N <N 0,为有限寿命区。在S-N 曲线的倾斜部分,与给定的循环数相对应的应力为有限寿命疲劳极限,又称条件疲劳极限。在有限寿命区内,当N 低于104~105时为低周疲劳区。
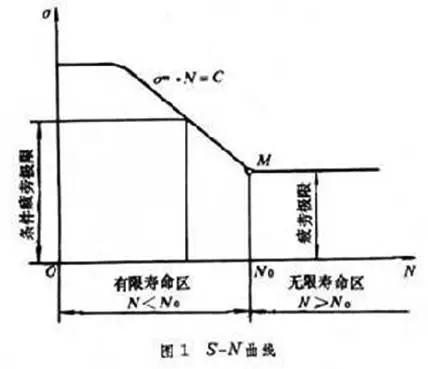
疲劳极限(σ-1);B点为a接近于零时的疲劳极限,它等于材料的强度极限(σ+1=σb);C点为脉动循环的疲劳极限(σ0 )。曲线上的其他点(如D点)表示其他循环特征的疲劳极限(σr)。
在工程上,常将这曲线简化为 ACB折线;在试验数据缺乏时,甚至简化为AB直线。这样简化,降低了设计计算的精确度,但偏于安全。常规疲劳强度设计是以名义应力为基础的,可分为无限寿命设计和有限寿命设计。
无限寿命设计 将工作应力限制在疲劳极限以下,即应用S-N 曲线的水平段进行设计,零件的疲劳寿命假设是无限的。
在疲劳试验中,除少数试样与实际零件相同外,一般使用小直径 (5~10毫米)、规定表面粗糙度的光滑试样。实际零件常存在由圆角、键槽等引起的应力集中,其尺寸和表面状态与试样有差异,所以,设计时必须引入应力集中系数 K、尺寸系数θ和表面系数β。有应力集中时K>1.0;零件尺寸大于试样尺寸时θ<1.0;表面粗糙度高于规定值时β<1.0。用表面强化方法,如表面热处理和表面冷加工硬化等,可使β 增大到1.0以上。
有限寿命设计 某些机械产品,例如飞机、汽车等,因为技术发展快、更新周期短,不需要很长的使用寿命;另一些产品,如鱼雷、导弹等,则是一次消耗性的。对于这些产品,减轻重量是提高其性能水平的关键。因此,即使整台产品需要较长寿命,也宁愿以定期更换的办法让其某些零件设计得寿命较短而重量较轻。有限寿命设计为保证使用寿命的条件下,采用超过疲劳极限的工作应力,以减小零件截面,减轻重量。
设零件承受循环应力,当其最大和最小应力的数值固定不变时,有限寿命设计的方法与无限寿命设计相同,只是在强度判据中,以有限寿命的条件疲劳极限替代疲劳极限。K、θ、β 等影响系数,也需使用相应寿命下的数值。
但是,大多数机械零件的循环应力,其最大和最小应力值是变化的,需要根据载荷谱(见载荷)用线性损伤积累理论进行寿命估算。
疲劳强度可靠性设计 在规定的寿命内和规定的使用条件下,保证疲劳破坏不发生的概率在给定值(可靠度)以上的设计。机械产品的可靠性设计是考虑机械及其零件的载荷和材料强度的随机性以及设计数据的分散性,用概率统计的方法进行,其中疲劳试验数据的分散性是它所考虑的一个重要方面。
新领域 疲劳强度设计的新领域包括:由反复的塑性应变产生的低周疲劳;由反复加热和冷却引起热应力循环的热疲劳;应考虑蠕变影响的在高温下受循环应力的零件的高温疲劳;由腐蚀和疲劳联合作用所引起的腐蚀疲劳。在这些领域中,已提出某些裂纹形成和扩展的模型,但要将这些模型实际应用于疲劳强度设计,还需做更多的工作。
参考书目
徐灏:《疲劳强度设计》,机械工业出版社,北京,1981。